Pre-stretch mechanism of pallet wrapping machine
The packaging of the pallet wrapping machine must be stretched, and the stretching methods of the pallet mechanical wrapping package include post-stretching and pre-stretching. There are two types of pre-stretching, one is roller pre-stretching and the other is electric pre-stretching. Post-stretching is done between the pallet and the stretch film roll on the machine. This method has a low stretch ratio (about 15% to 20%). If the stretch ratio exceeds 55% to 60%, it exceeds the original yield point of the film, the film width is reduced, the puncture function is also lost, film is easy to break. Besides, at 60% stretch rate, the pulling force is still very large. And for fragile goods, it can deform the goods.
Pre-stretching is done by two rolls. The two rollers of the roller pre-stretching are connected together by a gear unit. The stretching ratio can be different according to the gear ratio. The tension is generated by the turntable, because the stretching occurs in a short interval, and the friction between the rollers and the film is generated. It is also large, so the width of the film does not shrink, and the original puncture function of the film also persists. No stretching occurs during actual wrapping of the pallets, which reduces the breakage caused by sharp edges or corners, and this pre-stretching can increase the stretching ratio to 110%.
The stretching mechanism of electric pre-stretching is the same as that of roller pre-stretching. The difference is that the two rollers are driven by electrical motor, and the stretching has nothing to do with the change of the turntables. Therefore, the flexibility is stronger, and it is suitable for light, heavy and irregular goods. Because of the low tension during packaging, the pre-stretching ratio of this method is as high as 300%, which greatly saves materials and reduces costs. The suitable film thickness is 15-24 μm.
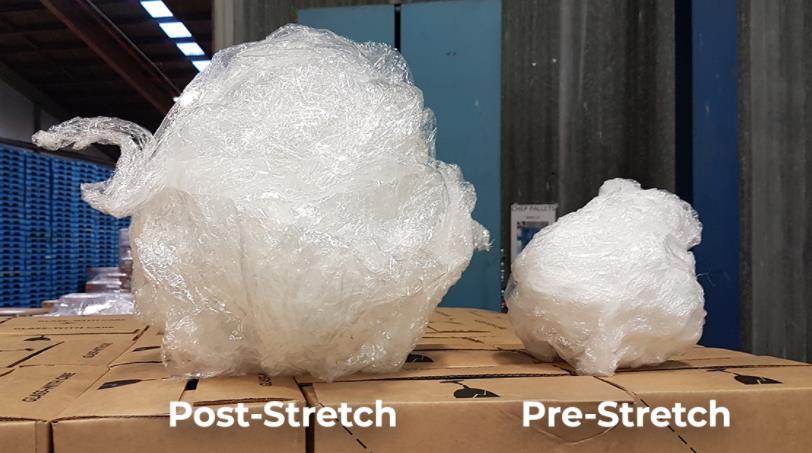
The use of this pre-stretch mechanism not only makes the pallet more tightly wrapped, improves it’s loadability. It also has reduced the consumption of packaging material in great amount, which means less plastic material will end up in landfill. It’s environmentally friendly and very cost saving.