How photoelectric sensor used on orbital stretch wrap machine?
Horizontal orbital stretch wrap machine refers to the ring rotating system around the goods moving horizontally at a constant speed, and at the same time adjusts the tension of the packaging material through the stretching mechanism to pack the object into a tight whole, and forms a spiral regular packaging on the surface of the object. It is the winding packaging machine widely used in industries such as plastic profiles, aluminum profiles, plates, pipes, and dyed fabrics.
Horizontal orbital stretch wrap machine, including a base, an operating room, a bracket and two conveying frames are installed on the upper part of the base, and several conveying rollers are installed in parallel on each transporting frame, and the two conveying frames are located on both sides of the operating room and one end extends into the frame. Inside, the bracket is located inside the operating room. Several sliding rollers are installed on one side of the bracket, and a packaging ring is installed between the sliding wheels. The other side of the bracket is installed with a motor frame, and a stepping motor is installed on the motor frame.
The maintenance door of the operating room of the existing horizontal stretch wrapping machine can be opened at will, and when the horizontal stretch wrapping machine is running, the operator of the orbital wrapper is easily injured if he enters the operating room at will.
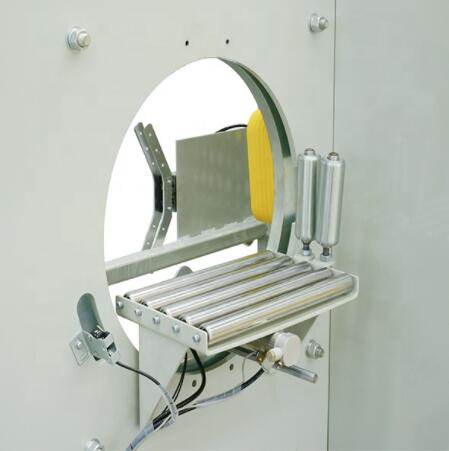
This is a device that locks the maintenance door of the operating room when the horizontal wrapping machine is running. It has the advantages of simple and compact structure, low manufacturing cost and easy use. The infrared laser emitter and infrared laser receiver can judge whether the sliding roller is rotating by monitoring the connecting rod constantly blocking the infrared laser between the infrared laser emitter and the infrared laser receiver when the horizontal stretch wrapping machine is running. When the laser transmitter and infrared laser receiver detect that the sliding roller is rotating, the infrared laser transmitter and infrared laser receiver transmit electrical signals to the industrial control instrument, and the industrial control instrument does not supply power to the electromagnet. At this time, the fixed block is located at the second fixed position. The maintenance door cannot be opened at this time. When the infrared laser emitter and the infrared laser receiver detect that the sliding spoke wheel does not rotate within two minutes, when the infrared laser emitter and the infrared laser receiver detect that the sliding roller is rotating, the infrared laser emitter and the infrared laser receiver The electric signal is transmitted to the industrial control instrument, and the industrial control instrument supplies power to the electromagnet. At this time, the electromagnet attracts the iron core, so that the fixing block is separated from the second fixing slot, and the maintenance door can be opened at this time. A new type of stepping motor can drive the sliding roller to rotate, thereby driving the packaging ring to rotate.